In PCB etching processes, the choice of etchant directly impacts production efficiency and product quality. In recent years, potassium monopersulfate (KMPS) has often been labeled as "more efficient and eco-friendly" and promoted by some manufacturers as a preferred alternative to traditional sodium persulfate (SPS). However, a deeper analysis of practical industry applications reveals that sodium persulfate remains the top choice for most PCB manufacturers.
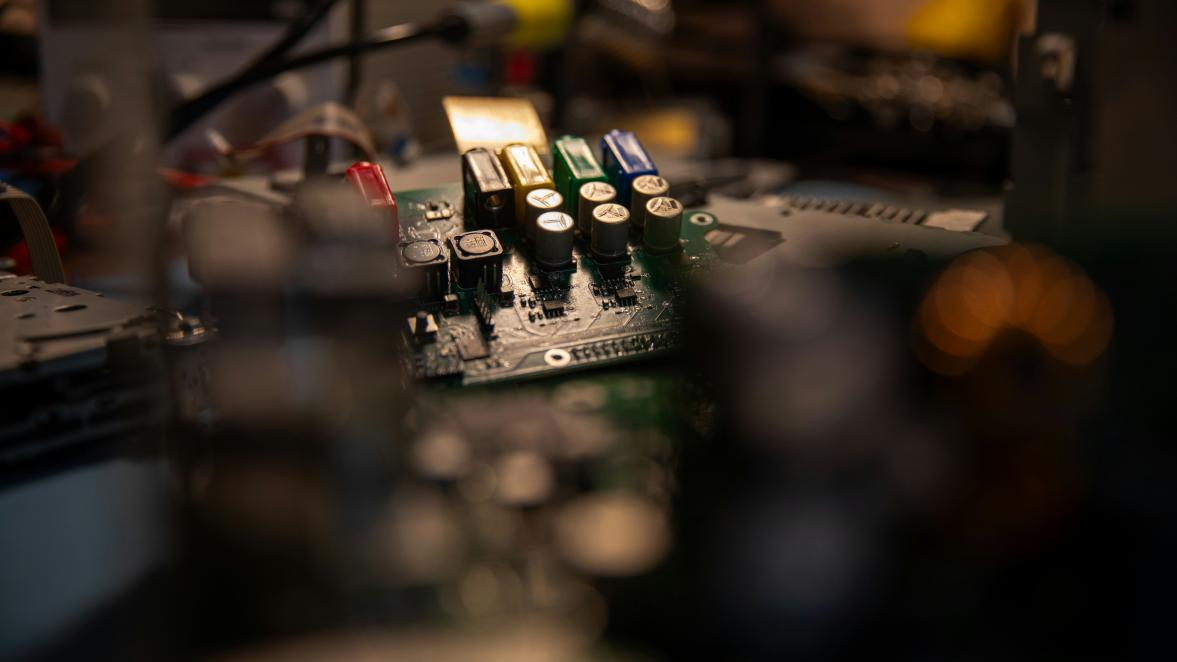
Ⅰ. "High Efficiency" Claims: KMPS Offers Little Advantage
While potassium monopersulfate may exhibit faster etching rates in laboratory settings, in actual mass production of PCBs, etching time is typically determined by the overall production line process rather than the reaction speed of a single chemical. Sodium persulfate can achieve efficiency comparable to KMPS by adjusting concentration and temperature. Moreover, KMPS’s high reactivity may cause problems: it easily leads to over-etching, affecting dimensional control of fine circuits and increasing the risk of scrapping.
In surface treatment, some KMPS manufacturers claim it delivers more uniform copper surface roughness. However, sodium persulfate, when paired with suitable additives (e.g., corrosion inhibitors, surfactants), can also achieve ideal surface results at a lower cost. Fujian ZhanHua Chemical, with extensive experience in sodium persulfate production, offers products that perform stably in actual manufacturing, helping manufacturers balance etching quality while better controlling production rhythms.
Ⅱ. Exaggerated Eco-Friendliness: KMPS Entails Higher Treatment Costs
Eco-friendliness is a key consideration in manufacturing. KMPS is marketed as a greener option, but the reality is more complex. Its wastewater contains high levels of sulfate and potassium ions, and its strong oxidizing properties result in high chemical oxygen demand (COD), making wastewater treatment more costly. In contrast, sodium persulfate wastewater treatment technologies are mature, with many manufacturers adopting stable recycling or neutralization solutions, leading to lower overall environmental costs. Fujian ZhanHua Chemical’s ultra-low chlorine, high-purity sodium persulfate excels in eco-performance, meeting most manufacturers’ environmental requirements while effectively controlling treatment expenses.
Additionally, KMPS’s "halogen-free" claim holds little significance for most PCB factories. Unless clients explicitly require halogen-free processes, sodium persulfate’s trace halogen residues do not affect PCB performance, yet KMPS’s high costs for this feature fail to yield corresponding market returns.
Ⅲ. Poor Stability: KMPS Creates Production Headaches
Stability of etchants is critical in production, and KMPS has clear shortcomings here. It easily degrades in high-temperature or humid environments, even undergoing self-decomposition—leading to bag swelling, heat release, and other issues—undoubtedly increasing storage management costs and complexities. Sodium persulfate, with much greater chemical stability, can be stored long-term under normal conditions, reducing waste from product degradation. Fujian ZhanHua Chemical’s sodium persulfate products, with their excellent stability, minimize unexpected production interruptions, supporting manufacturers in improving efficiency.
Ⅳ. Persistent High Costs: KMPS Lacks Cost-Effectiveness
Cost is a critical factor for enterprises, and KMPS is at a clear disadvantage. Its market price is typically higher than SPS. While some manufacturers claim KMPS requires lower dosage, its rapid decomposition and activity decay in actual production often necessitate higher concentration replenishments, ultimately increasing costs.
Moreover, switching from SPS to KMPS requires adjusting chemical formulations, equipment parameters, and even replacing corrosion-resistant materials. These adjustments consume time and resources, further raising production costs. Fujian ZhanHua Chemical’s sodium persulfate, while ensuring quality, offers greater price competitiveness. Its stable performance adapts to mature industry application schemes, helping PCB manufacturers control costs and enhance production value.
Ⅴ. Industry Preference Remains: SPS Is Still the Preferred Choice
Currently, over 90% of PCB manufacturers continue to use sodium persulfate, a statistic that underscores its industry recognition. Except for a few manufacturers producing high-end HDI boards, most PCB enterprises—especially those in consumer electronics and automotive electronics—prioritize SPS for its superior overall cost-effectiveness. As a key player in sodium persulfate production, Fujian ZhanHua Chemical remains committed to technological innovation and product optimization. Its sodium persulfate products precisely meet etching needs for different PCB types, providing the industry with consistent high-quality solutions.
In PCB etching, while KMPS has limited advantages in specific scenarios (e.g., ultra-high-precision HDI boards), sodium persulfate outperforms in critical areas such as efficiency, eco-friendliness, stability, and cost. For most PCB manufacturers, sodium persulfate remains the more economical, stable, and reliable choice.